阜新非標(biāo)硬質(zhì)合金錘頭廠
發(fā)布時(shí)間:2023-04-24 00:30:05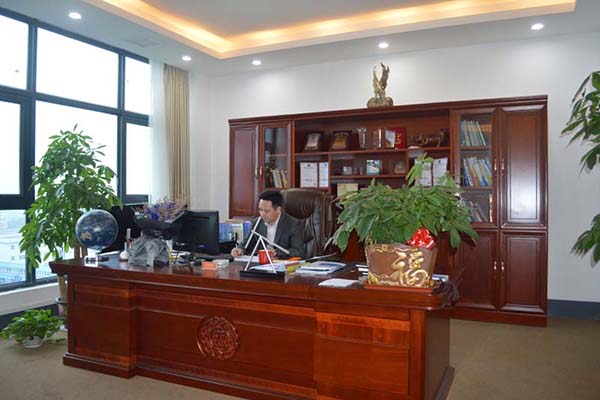
阜新非標(biāo)硬質(zhì)合金錘頭廠
硬質(zhì)合金長(zhǎng)條性能:硬質(zhì)合金長(zhǎng)條具有很好的硬性、高硬度、耐磨性好、高彈性模量、高抗壓強(qiáng)度、化學(xué)穩(wěn)定性好(耐酸、堿、高溫氧化)、沖擊韌性較低、膨脹系數(shù)低,導(dǎo)熱、導(dǎo)電與鐵及其合金相近的特點(diǎn)。硬質(zhì)合金長(zhǎng)條應(yīng)用范圍:硬質(zhì)合金長(zhǎng)條具有紅硬性高、焊接性好、高硬度、高耐磨性的特征,主要應(yīng)用于制作加工實(shí)木、密度板、灰口鑄鐵、有色金屬材料、冷硬鑄鐵、淬硬鋼、PCB、制動(dòng)材料。使用時(shí)應(yīng)具體根據(jù)用途選擇合適材質(zhì)的硬質(zhì)合金長(zhǎng)條。

阜新非標(biāo)硬質(zhì)合金錘頭廠
硬質(zhì)合金球齒具有優(yōu)越的耐磨性及沖擊韌性,與同類產(chǎn)品比具有更高的鉆掘速度。不磨球齒系列釬頭鈍化使用周期長(zhǎng),其壽命約為磨次同直徑刃片頭釬頭壽命的5-6倍,有利于節(jié)省輔助工時(shí),減輕工人體力勞動(dòng)和加快工程速度。硬質(zhì)合金球齒具有其獨(dú)特的工作性能,因此被廣泛應(yīng)用于石油鉆探和鏟雪,雪犁機(jī)器等設(shè)備。此外,硬質(zhì)合金球齒在切削工具與礦山機(jī)械、道路維修和煤鉆工具中也有很好地應(yīng)用。礦山用硬質(zhì)合金球齒主要用作采石、采礦以及隧道和民用建筑中的采掘工具。
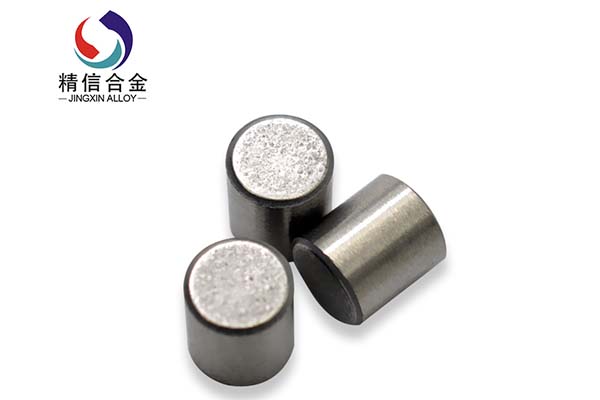
阜新非標(biāo)硬質(zhì)合金錘頭廠
硬質(zhì)合金是通過粉末冶金工藝由難熔金屬和結(jié)合金屬的硬質(zhì)化合物制成的。它是具有極高硬度的合金材料。具有一系列優(yōu)異的性能,例如高硬度,耐磨性,良好的強(qiáng)度和韌性,耐熱性和耐腐蝕性,尤其是其高硬度和耐磨性,它在1000°C時(shí)仍具有高硬度。鎢鋼也稱為鎢鈦合金或高速鋼或工具鋼。硬度為維氏10K,僅次于金剛石。鎢鋼和硬質(zhì)合金具有很高的硬度,耐磨性,強(qiáng)度和韌性,耐熱性和抵抗性。鎢鋼的優(yōu)點(diǎn)在于其高硬度和耐磨性。即使在1000℃,它仍然具有很高的硬度。

阜新非標(biāo)硬質(zhì)合金錘頭廠
硬質(zhì)合金模具操作人員必須特別注意模具規(guī)劃中的幾個(gè)重要方面:當(dāng)規(guī)劃級(jí)進(jìn)模時(shí),模具壓料受力平衡,以避免當(dāng)帶材沒有進(jìn)入模具時(shí),模具產(chǎn)生傾斜。裝置足夠的模具保護(hù)裝置,如接近開關(guān)和雙層金屬傳感器。模具在側(cè)沖或旁邊面成型時(shí)產(chǎn)生大量的側(cè)推力,模具規(guī)劃應(yīng)該考慮吸附這些旁邊面受力。模具入口添加導(dǎo)料槽引導(dǎo)資料更簡(jiǎn)單進(jìn)入模具。

阜新非標(biāo)硬質(zhì)合金錘頭廠
溫度越高,溶解和擴(kuò)散速率就越快,被一定量的Co溶解的WC就越多,即細(xì)WC向粗WC遷移的速度加快。過高的燒結(jié)溫度易產(chǎn)生異常的晶粒長(zhǎng)大。在較低溫度下延長(zhǎng)燒結(jié)時(shí)間,同樣可以使晶粒長(zhǎng)大??梢姛Y(jié)溫度和時(shí)間可以互補(bǔ)。通過調(diào)整溫度或時(shí)間可以獲得相同的WC晶粒度。燒結(jié)溫度對(duì)碳化鎢晶粒長(zhǎng)大的影響。平均粒度增大時(shí),晶粒長(zhǎng)大迅速下降,平均粒度為3um或3um以上時(shí),晶粒長(zhǎng)大對(duì)燒結(jié)溫度不大敏感,在很寬的燒結(jié)溫度范圍內(nèi),其粒度或機(jī)械性能變化很小。

阜新非標(biāo)硬質(zhì)合金錘頭廠
化學(xué)拋光:化學(xué)拋光是讓硬質(zhì)合金模具在化學(xué)介質(zhì)表面微觀凸出部分優(yōu)先溶解,從而得到平滑面。這種方法可拋光形狀復(fù)雜的工件。得到的表面粗糙度一般為10μm。電解拋光:電解拋光的原理和化學(xué)拋光相同,都是溶解材料表面微小凸出部分,使表面光滑。超聲波拋光:超聲波拋光是把工件放入磨料懸浮液中并一起置于超聲波場(chǎng)中,依靠超聲波的振蕩作用,使磨料在工件表面磨削拋光。超聲波拋光可以不讓其腐蝕,利于表面亮化。流體拋光:流體拋光是依靠高速流動(dòng)的液體及其攜帶的磨粒沖刷工件表面達(dá)到拋光的目的。常用方法有:磨料噴射加工、液體噴射加工、流體動(dòng)力研磨等。